Microfilm, Famac, Evolution Tech. Tre diversi interlocutori uniti per sviluppare un progetto avanguardistico che permette di ridurre chimica, inquinamento, costi e scarti.
Per noi di Tannery International è importante entrare nelle aziende che raccontiamo. Approfondire progetti e processi, guardare dal vivo macchinari di ultima generazione e ascoltare pareri di differenti interlocutori è di grande importanza, oltre che di interesse. Nelle pagine vi illustreremo la nostra giornata ad Arzignano presso le sedi di Microfilm, Famac ed Evolution Tech dove abbiamo scoperto tre convinti promotori della rivoluzione tecnologica green.
Le sfide del 21° secolo a cui il settore della pelle è sottoposto sono molteplici e non di poco conto: tecnologie innovative, materie prime di alta qualità di origine naturale, energia derivata da fonti rinnovabili, eliminazione dell’inquinamento, miglioramento continuo e la soddisfazione delle esigenze dei consumatori sono diventati i principali focus intorno ai quali si muovono sempre più aziende, consce dei pericoli derivanti dall’impatto ambientale delle singole attività produttive. La crescente consapevolezza che uno sviluppo sostenibile, inteso come equilibrio tra sfruttamento delle risorse, salvaguardia del pianeta e pianificazione del futuro sia obbligatorio, sta influenzando profondamente il cambiamento di mentalità che ha dato il via a una nuova e moderna rivoluzione industriale. Tre le realtà promotrici di questa trasformazione ve ne sono tre ubicate nella zona di Arzignano – Microfilm, Famac ed Evolution Tech – che hanno stretto una solida collaborazione per rispondere a una delle domande più attuali e importanti: come essere veramente green creando valore in tutta la filiera della pelle? Le normative ambientali sempre più stringenti, i consumatori sempre più attenti e i clienti internazionali, dei settori moda, automotive e arredo casa sempre più esigenti riguardo agli standard di sostenibilità, hanno reso urgente e imperativa la scelta di processi che facciano la differenza, svincolati da vecchie e obsolete dinamiche. Sappiamo che l’Italia è leader nel settore conciario, una delle componenti d’eccellenza della filiera del settore tessile-moda-abbigliamento, ma l’attivazione di progetti comuni non è ancora così naturale.
Microfilm, nome riconosciuto a livello internazionale per la produzione di film per la stampa a caldo, ha compreso da tempo che l’introduzione di cambiamenti pro-ecologici nel settore è possibile. MicroBase, novità di quest’anno, rappresenta in questo senso una assoluta rivoluzione: non è solo un prodotto ma un intero sistema che consente di rispondere alle esigenze di quei conciatori e rifinitori che non si accontentano delle soluzioni convenzionali. Parliamo di un nuovo foil a base acqua che, grazie alla sua tecnologia e al suo spessore di soli 3 micron, è in grado di creare un primo strato uniforme sulla pelle, consentendo di ottenere una superficie totalmente omogenea e coprente. Questo nuovo metodo, che sostituisce la tradizionale copertura del fondo (base coat), evita di bagnare la pelle mantenendola più morbida e permettendo, soprattutto, che i difetti vengano nascosti e non sia evidenziato il cambio colore prodotto dal differente assorbimento. La pelle così “filmata” e resa uniforme dalla base poliuretanica agevola inoltre tutte le lavorazioni successive: per esempio si può procedere con la stampa diretta, dopo averla isolata unicamente con un prodotto a spruzzo; la pelle “rimonta” si può rifinire per poi essere stampata; oppure, qui entra in gioco per la prima volta Evolution Tech, può essere stampata con il suo nuovo brevetto con cilindro a freddo. È dunque chiaro che, oltre a rappresentare la copertura ideale, MicroBase è la soluzione perfetta per risparmiare in chimica, ridurre gli scarti e diminuire l’inquinamento (anche aereo) in modo esponenziale. Infine, per merito di Famac, consulente nello studio delle possibili applicazioni, è emerso che non è necessario preparare la pelle con resine o altri prodotti chimici ma basta che sia calda e senza umidità superficiale nel momento dell’accoppiamento, processo reso possibile da Evolution Tech grazie al brevetto di un inedito tappeto di introduzione preriscaldato che porta la pelle a temperatura e contemporaneamente effettua l’accoppiatura con MicroBase.
LA PAROLA AI PROTAGONISTI
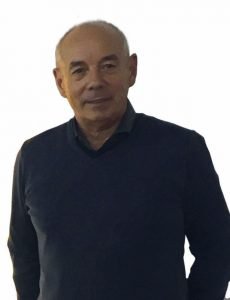
GIULIANO SAMBUGARO DI MICROFILM
MICROFILM Srl nasce nel 1997 a Brendola, in provincia di Vicenza, da un’idea di Giuliano Sambugaro, forte di diversi anni di esperienza nel settore della rifinizione. Da allora l’azienda ha continuato a evolversi, continuando a fare passi da gigante e dotandosi nel 2006 di un impianto speciale per laminati totali e parziali destinati al pellame.
Come è nata questa sinergia? Ernesto Salvioni di MICROFILM: “Siamo sempre stati convinti che l’unione fa la forza. Siamo parte dell’insieme, non siamo tutto. Collaborare significa essere capaci di affrontare e vincere le sfide che il mercato presenta quotidianamente. La nostra sinergia ci ha permesso di sviluppare intuizioni nuove, creare progetti condivisi e avere processi più veloci ed efficienti. Da idee nuove nascono opportunità nuove. Sono sincero, da soli non saremmo arrivati a sviluppare un prodotto così innovativo in tempi così rapidi”.
Facciamo un passo indietro. Chi è stato l’iniziatore di questa rivoluzione? “Tutto è partito da una richiesta di Angelo Cozza, della Famac, e da alcuni suoi clienti rifinitori, decisi a ridurre l’impatto ambientale delle loro lavorazioni e a migliorate la qualità del prodotto finito”.
Giuliano Sambugaro: Passo dopo passo avete integrato una serie di prodotti che vi hanno portato a questo risultato particolare, corretto? “Esatto. Evolution Tech possedeva già una macchina con sistema di preriscaldamento che avevamo testato su altri prodotti con risultati molto buoni, con il prodotto Microbase i risultati sono stati eccezionali. Al momento stiamo mettendo a punto un sistema di stacco automatico delle pelli che verrà implementato sulla nuova macchina che Evolution Tech sta costruendo. Come potete immaginare avrà un sistema fatto su misura per MicroBase ma che potrà essere tranquillamente utilizzato anche per altri prodotti”.
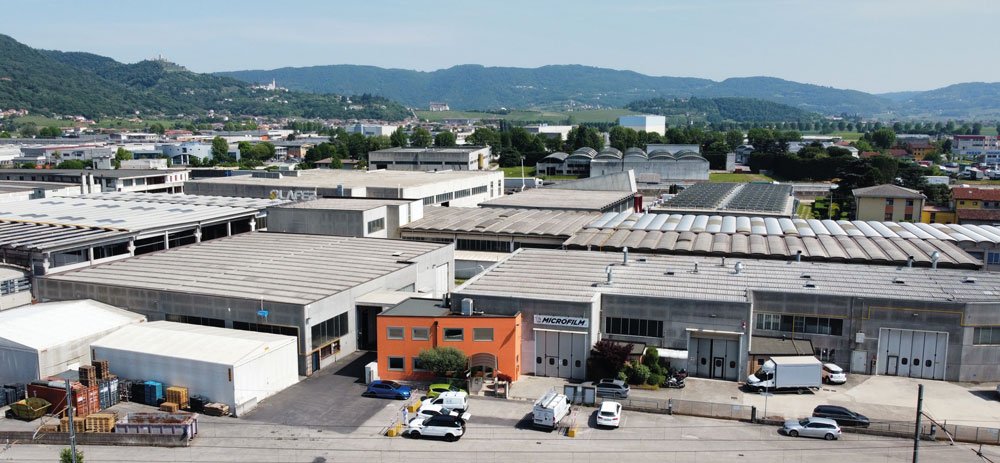
La sede Microfilm a Brendola (VI)
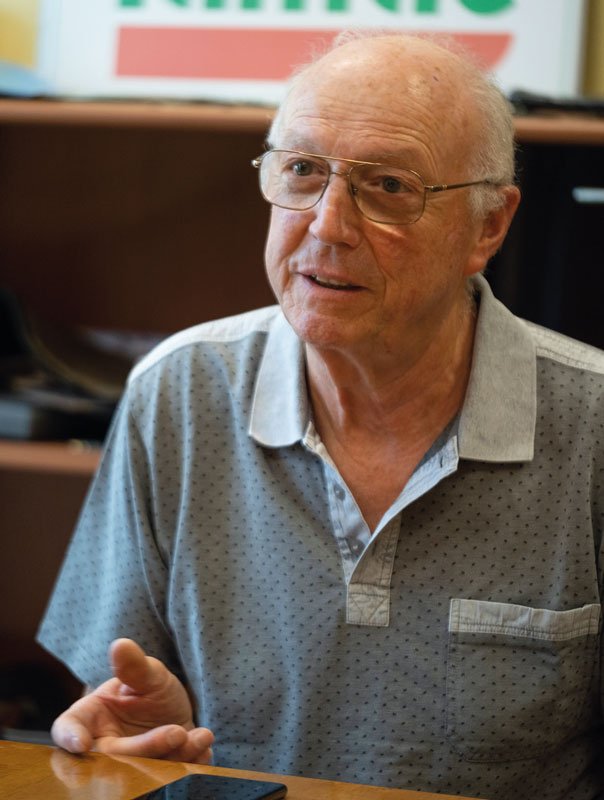
ANGELO COZZA DI FAMAC
Quando è nata la vostra azienda e che crescita ha avuto?
“Io e mia figlia abbiamo fondato la società nel 1997. Nasco come elettricista ma poco dopo mi appassiono di meccanica che non ho mai più lasciato. Tutto ciò che è presente oggi in azienda è una mia costruzione. Dopo 15 anni trascorsi all’interno della Ge.ma.ta come tecnico, montatore e professionista del servizio post vendita, a causa della sua scissione, mi sono spostato in Rollmac, il cui titolare era mio cognato. A 50 anni, sempre con la cassetta dei ferri in mano, ho deciso di iniziare un percorso imprenditoriale e mi sono rimboccato le maniche”.
Qual è stata la prima macchina che ha progettato e com’è nata?
“Era più o meno il 1995. Un giorno ero a Turbigo in una conceria che realizzava capretti di alto livello e mi chiesero: “Perché noi applichiamo le carte a caldo e voi che fate le macchine col cilindro a caldo non riuscite a farne una per soddisfare le nostre esigenze?”. Mi ricordo di avergli risposto subito di dirmi cosa gli serviva che ci saremmo messi all’opera. Così è nata la prima macchina col cilindro in teflon riscaldato per applicazione di carte. La macchinava funzionò ma ebbe bisogno poco dopo di una modifica al cilindro perché era troppo piccolo per le loro esigenze. Ne creammo subito una nuova, dotata di un cilindro di dimensioni più rilevanti con una nuova struttura che consentisse di lavorare con pellami più grandi e a velocità maggiori, e un revolver per lavorare con quattro o cinque disegni alla volta senza la necessità di cambiare il rotolo. Sono stati tutti accorgimenti che piano piano ci hanno portato a sviluppare l’ultima nata”.
Come siete arrivati ad occuparvi dell’applicazione di transfert cere, lamine e paillettes per pelli e tessuti?
“Poiché qui in zona, ad Arzignano, non c’era nessuno che lo faceva. Mi sono detto, “perché non provare?”. È stata una scommessa col diavolo perché non sapevamo come sarebbe andata. Il coraggio ci ha premiati”.
Come siete arrivati a utilizzare il sistema MicroBase ideato da Microfilm?
“I vantaggi di questo film, a parità di alti standard qualitativi, rispetto a una rifinizione normale, sono enormi in termini di risparmio di prodotti chimici ed acque (-70%). Quando noi andiamo a rifinire una pelle e cominciamo a spruzzare il materiale per coprire i difetti, bagniamo la pelle mettendoli in realtà in risalto perché o diventano scuri, o diventano chiari. Col sistema MicroBase noi applichiamo un film che, sfruttando il termoadesivo, fonde all’interno della pelle e non bagna le superfici. Così il colore originale rimane inalterato. Poi da lì a portarla a colore basta 1/3 del materiale chimico normalmente utilizzato. Tanto per darvi una idea, per rifinire una pelle di carrozzeria attualmente si usano 30 grammi al metro quadro di prodotto, mentre con questo sistema siamo arrivati a rifinirli con soli 6 grammi, un quinto in meno”.
Che altri plus ha MicroBase?
“Per esempio, quando andiamo a rifinire la pelle abbiamo un ulteriore risparmio perché il fondo è già chiuso e l’assorbimento della pelle è uguale dal filone al fianco, perciò viene ottimizzato sia il taglio che la rifinizione. Quello che è sorprendente è che quando si piegano le pelli non si vede la grogliatura, ovvero le pieghe che naturalmente si formano”.
Significa anche meno materia prima buttata…
“Esatto perché anche gli scarti diminuiscono. Sapete già che nei calzaturifici, o dove fanno le selle da cavallo, prendono la pelle e la posizionano su un mezzo bottale, la bloccano e la mettono in tensione. Se la pelle presenta un difetto viene subito messo in evidenza. Con questo sistema invece non accade perché l’elasticità del film è superiore all’elasticità della pelle. Quando si mette in tensione, il difetto anziché vedersi tende a scomparire, non lo si vede più. Chi riesce a intendere cosa fa questo film ha vinto!”.
La macchina esiste già?
“E’ già in produzione con ottimi risultati e stiamo lavorando tutti insieme alla sua realizzazione definitiva. Siamo partiti con una spalmatura del film a 1,60 mt, in altezza, ma le esigenze delle aziende nel nostro distretto sono diverse perché hanno necessità di lavorare su pelli intere. Perciò il nostro sforzo è stato quello di realizzare una macchina che lavori a 3200. Non vi nego che abbia perso qualche ora di sonno…(ride). Quando si fanno i test può accadere davvero di tutto ma abbiamo cominciato a vedere i primi frutti. In Turchia stanno sperimentando un processo differente: hanno cominciato a tagliare le pelli prima di lavorarle. Per capirne il motivo bisogna pensare all’intero processo: quando utilizziamo la pelle grezza, tolto tutto ciò che va scartato al finale, se facciamo i conti cosa accade? Io taglio la pelle, faccio gelatina e qualcosa recupero. Se io parto da una pelle finita, alla quale viene fatta la concia, la riconcia, la tintura, l’ingrasso, la rifinizione, che comunque va tagliata comunque perché non si utilizza, diventa un rifiuto speciale. I più grossi conciatori turchi hanno già installato impianti per realizzare le gelatine in casa e, tagliando le pelli, fanno uscire il 25% in meno di peso. Nei container ci sta più materiale; quando si va alla concia, non devi lavorare pelle che poi va buttata via. Potete immaginare che impatto abbia sui costi e di conseguenza sul risparmio finale”.
Questo cosa accade in Turchia e non in Italia? Perché?
“Perché i tempi qui non sono ancora maturi. Non tutti sono pronti a collaborare insieme come abbiamo fatto noi e guardare oltre, verso un bene comune più alto e con maggior lungimiranza. Dobbiamo diminuire gli scarti, questo è un tema fondamentale”.
È un progetto eccezionale sulla carta ma che aspettative avete per il futuro?
“Sono sicuro che, non appena arriverà la prima 3200 che sarà in grado di lavorare addirittura con rotoli da 5 mila o 6 mila metri, avremo le nostre soddisfazioni… A parte la battuta, ci sarà uno sviluppo incredibile. È un dato di fatto. Questo è il futuro”.
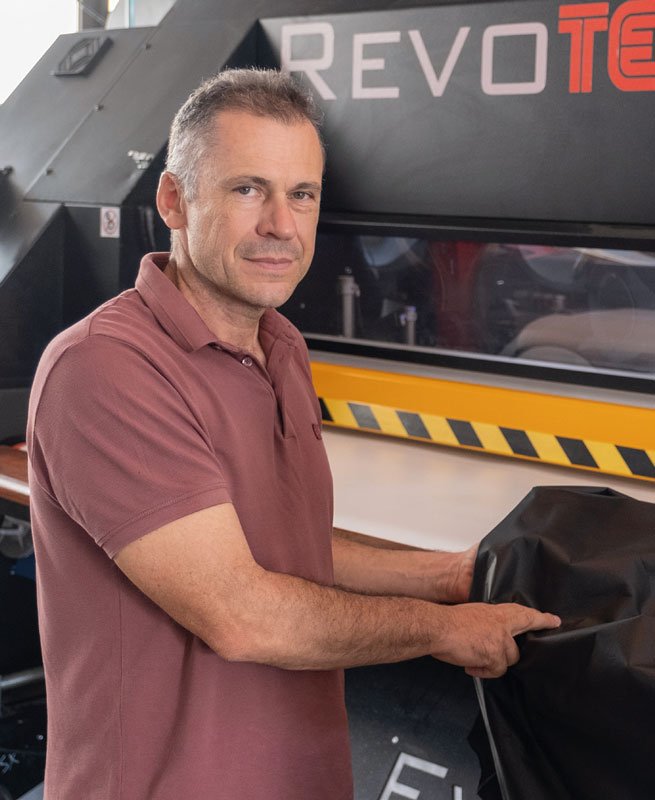
ANTONELLO MARCHINO DI EVOLUTION TECH
Ci racconta le origini della vostra azienda?
“Ho iniziato a lavorare con EmmeZeta RotoPress ancora quando le due ditte lavoravano insieme. Successivamente sono passato in Feltre per altri sette anni, dopodiché, insieme ad altri due colleghi, un programmatore e un disegnatore, Alberto Pavan e Denis Lovato, e ad alcuni finanziatori, abbiamo fondato Evolution Tech. Grazie alle nostre idee e alla loro complicità economica, siamo riusciti ufficialmente a partire nel 2016. Da qui è stata una continua progressione. Abbiamo scelto il nome di Evolution Tech proprio perché la nostra filosofia è stata sin dall’inizio quella di voler creare sempre qualcosa di nuovo. Abbiamo già sviluppato in house più di sette brevetti, alcuni internazionali, merito dei quali possiamo garantire prodotti diversificati e più tecnologici. La condivisione con Microfilm e con Famac è per noi fondamentale perché questo quartetto, di chimica, macchine, operatore e infine di rifinizione, rappresenta un progetto del tutto completo”.
Avete intercettato uno spazio libero che mancava e avete introdotto tutta una serie di tecnologie brevettate che vi hanno portato un passo avanti…
“Sì, abbiamo iniziato con macchine totalmente 4.0. Le prime erano da stampa, che rimane il nostro focus primario, e poi siamo passati alle macchine da stiro. Adesso, grazie a questa bellissima collaborazione, partiamo da ultimi, ma non in termini di qualità, perché la tecnologia che stiamo utilizzando in tutti i tre settori, in tutti e tre i vari comparti, è al massimo livello”.
Facendo i primi esperimenti a che benefici avete assistito?
“A benefici molto importanti. Abbiamo già venduto cinque macchine per il progetto MicroBase: quattro in Toscana e una in Polonia, tre 1800 tranne l’ultima nata che è una 3200”.
E che feedback avete avuto?
“Molto buono. Il vantaggio di questo film è la possibilità di essere utilizzato sia da piccoli operatori che da ditte che non hanno depuratori, che non hanno camini, che non hanno la possibilità di smaltire fumi, acque o quant’altro. Questo perché la pelle che arriva al destinatario è già preparata, non è bagnata, e il film, che è un altro materiale secco ha necessità di essere solo accoppiato. Non serve alcun abbattitore, nessun camino. Vi racconto un aneddoto divertente…. La macchina che abbiamo venduto in Polonia è stata acquistata da una famiglia composta di tre persone, suocero e i due coniugi, che si sono attrezzati con un po’ di crast di colori base e, man mano che arrivano i clienti conciatori polacchi della zona, prendono il film che desiderano e lo accoppiano quasi nello stesso momento. Se non è per lo stesso giorno, riescono a consegnare il giorno senza che i clienti debbano aspettare. Possiamo dire che è un vero e proprio just in time. Basta solo lo spazio dove alloggiare il macchinario e poco altro. Pensate cosa potrebbero fare le grandi aziende…”.
Che feedback vi ha dato invece il mondo della moda?
“Le concerie toscane mi hanno confermato che riescono ad avere una pelle molto più leggera dal punto di vista della pigmentazione, senza difetti (cosa che gli regala almeno un upgrade) e molto facile da lavorare”.
Il vostro personale feedback invece?
“Il nostro segreto, che vi sveliamo con piacere, è che insieme a Microfilm abbiamo potuto constatare che, utilizzando il nostro brevetto di preriscaldo, la pelle ha una tenuta molto maggiore. I vantaggi importantissimi di questo sistema sono in totale quattro. Il primo è che lavorando con la pelle calda la fusione con il film è perfetta. Il secondo vantaggio è che con questo nostro preriscaldo si elimina la presenza di umidità sulla superficie della pelle. Quando quest’ultima è presente, pericolosissima specialmente d’inverno, accade che normalmente tenda a rimanere incastrata tra film e pelle, creando quelle piccole bollicine che non vanno più via se non con un ulteriore processo di essicazione e di rilavorazione. Uno spreco in termine di energia e di tempo. Riassumendo, i primi due vantaggi sono un maggiore aggancio e la sicurezza di non avere umidità all’interno della pelle”.
Quali sono il terzo e quarto vantaggio?
“Un altro punto di forza è l’aumento della velocità con cui lavorano le macchine. Normalmente la pelle deve raggiungere la temperatura di trasferimento in un tempo brevissimo, un secondo circa. Tutto il calore necessario deve essere trasmesso dal cilindro riscaldato al momento del contatto. Se la pelle è già in temperatura la penetrazione degli adesivi è immediata, uniforme e profonda. Il quarto vantaggio è l’abbassamento delle temperature con cui si deve lavorare: abbiamo visto che, passando da una macchina tradizionale senza preriscaldo a una macchina con preriscaldo, riusciamo anche ad abbassare la temperatura del cilindro. Ciò significa un netto risparmio di energia elettrica. Infine, non meno importante, la pelle rimane più morbida perché con le alte temperature la pelle s’indebolisce perché soggetta a uno shock termico non indifferente. Il sistema MicroBase rappresenta secondo me un concreto un passo avanti per una nuova rifinizione bella e sostenibile”.
IL PARERE DEI RIFINITORI
I VANTAGGI DI MICROFILM RACCONTATI DA CHI LI USA
L’ultimo stadio delle lavorazioni delle pelli è quella che possiamo considerare il più artistico. Quando si parla di rifinizione il primo pensiero va alla serie infinita di passaggi a cui la pelle è sottoposta e a tutti i processi che sono coinvolti.
Come nasce la vostra collaborazione con Microfilm?
“Eravamo a conoscenza che Microfilm stesse lavorando da alcuni anni allo sviluppo di una nuova tecnologia che ci permettesse di migliorare la qualità del nostro lavoro sia quella delle pelli. Avevamo la necessità di trasformare un processo tradizionale di rifinizione in qualcosa di più performante sotto tanti punti di vista. Finalmente abbiamo raggiunto l’obbiettivo. In teoria tutti siamo capaci di far tutto ma in questo specifico caso questo risultato è stato possibile grazie all’esperienza delle persone coinvolte. Noi rifinitori siamo in grado di realizzare articoli di altissima qualità come la pelle anilina ma non solo. Utilizziamo altre tecnologie intelligenti ma che non sono adatte a tutto. Per esempio con la carta release, che è un applicato su bagnato, si può fare molto ma non copre tutte le nostre necessità, soprattutto sui montati”.
In cosa differisce questa nuova tecnologia?
“Quando lavoriamo con film spessi e lo posiziono sui difetti che la pelle ha, è come mettere l’asfalto su una pista di motocross, con tutto ciò che ne consegue. Quindi i difetti vengono solo coperti non “restaurati”. La ricerca è partita proprio da qui: volevamo qualcosa di molto più sottile con cui lavorare pelli intere, che avesse proprietà tecniche un po’ diverse da quello che c’è sul mercato e che garantisse, perché no, anche una qualità migliore. Utilizzare un film non è una novità, lo è MicroBase”.
MicroBase: che caratteristiche ha, a cosa serve e qual è la sua sostenibilità?
“Partiamo dal presupposto che oggi è anacronistico fare alcuni tipi di rifinizione e utilizzare macchine obsolete. Ci siamo resi conto che è già fin troppo tardi per una inversione di tendenza ma non si può far più finta di nulla. Poter usufruire di più possibilità è fondamentale. L’idea è quella di un film sottilissimo, 3 micron di spessore, che, una volta applicato, mi dia la possibilità di avere una superficie completamente omogenea senza assorbimenti diversi. Per cui, a parità di rifinizione, io darò sopra la pelle l’80/90% in meno di rifinizione. Per fare un esempio, la rifinizione di un articolo economico vuole 120/130 grammi di rifinizione per metro quadro mentre con questo sistema se ne utilizza 10 volte meno, scaricando nell’aria l’80% di inquinanti in meno. Specialmente negli smerigliati significa che la piega di volume del film è molto più fine perciò le pelli saranno molto più belle dal punto di vista estetico. Inoltre il poliestere su cui è applicato il film, una volta utilizzato, non viene buttato via ma si ripulisce e si ribobina una seconda volta per altri usi. Con le classiche release il problema più grosso è che per ogni metro prodotto quadrato di pelle c’è un metro quadrato di adesivo che poi va bruciato. Il sistema Microbase ha solo vantaggi perché dal punto di vista estetico e tecnico è una rivoluzione”.
Come testimoniano i rifinitori che lo hanno provato, oltre a migliorare l’estetica e la morbidezza delle pelli, il Sistema MicroBase RIDUCE considerevolmente:
- L’impatto ambientale
- L’inquinamento aereo
- L’utilizzo di prodotti chimici
- La quantità di scarti
- I costi di smaltimento dei rifiuti pericolosi
- I tempi di rifinizione
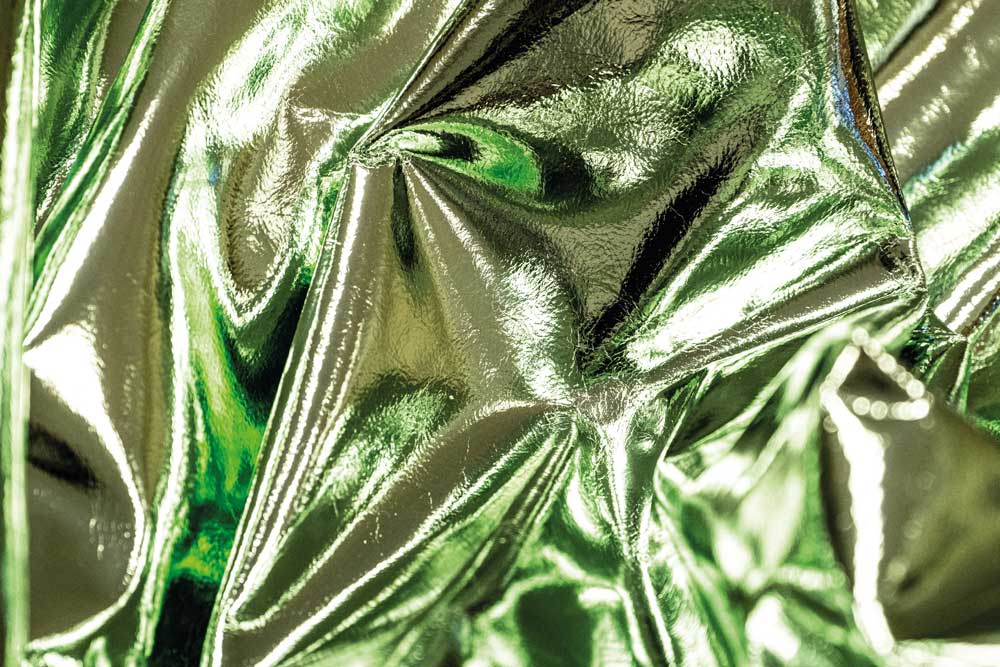