“La strategia giusta per imporsi nei mercati” - Todesco, azienda di Creazzo (Vicenza), propone il software Statwatch che monitora in tempo reale le prestazioni produttive
Piena fiducia nel programma di crescita pianificato negli ultimi anni a cui si aggiunge un’analisi approfondita dei mercati mondiali, con attenzione ai prezzi delle materie prime e ai costi di produzione ed energetici. È una strategia a 360 gradi, legata anche alle dinamiche non solo economiche, quella che viene portata avanti dai vertici aziendali della Todesco di Creazzo (Vicenza), specializzata nella produzione di linee di rifinizione intelligenti a servizio del comparto conciario, guidata dai fratelli Paolo e Giorgio Todesco. Con il primo, intervistato in sede a fine aprile, abbiamo analizzato la situazione del mercato e gli sviluppi futuri dell’azienda veneta.
“Per quanto ci riguarda – le parole di Paolo – il 2023 sarà un anno di crescita, dopo che in quello precedente abbiamo lavorato moltissimo dal punto di vista della ricerca e dello sviluppo. Nel 2022 i costi derivati dalle spese energetiche e la difficoltà di approvvigionamento delle materie prime hanno provocato un rallentamento degli investimenti di molte aziende del settore. A farne le spese è stata l’economia globale, già fiaccata negli ultimi tempi da fenomeni extra-economici come la pandemia sanitaria, il blocco cinese e la guerra in Ucraina. Anche per la nostra azienda c’è stato un rallentamento, già compensato con i primi mesi di quest’anno, visto che abbiamo ordini sino ad inizio della primavera 2024”.
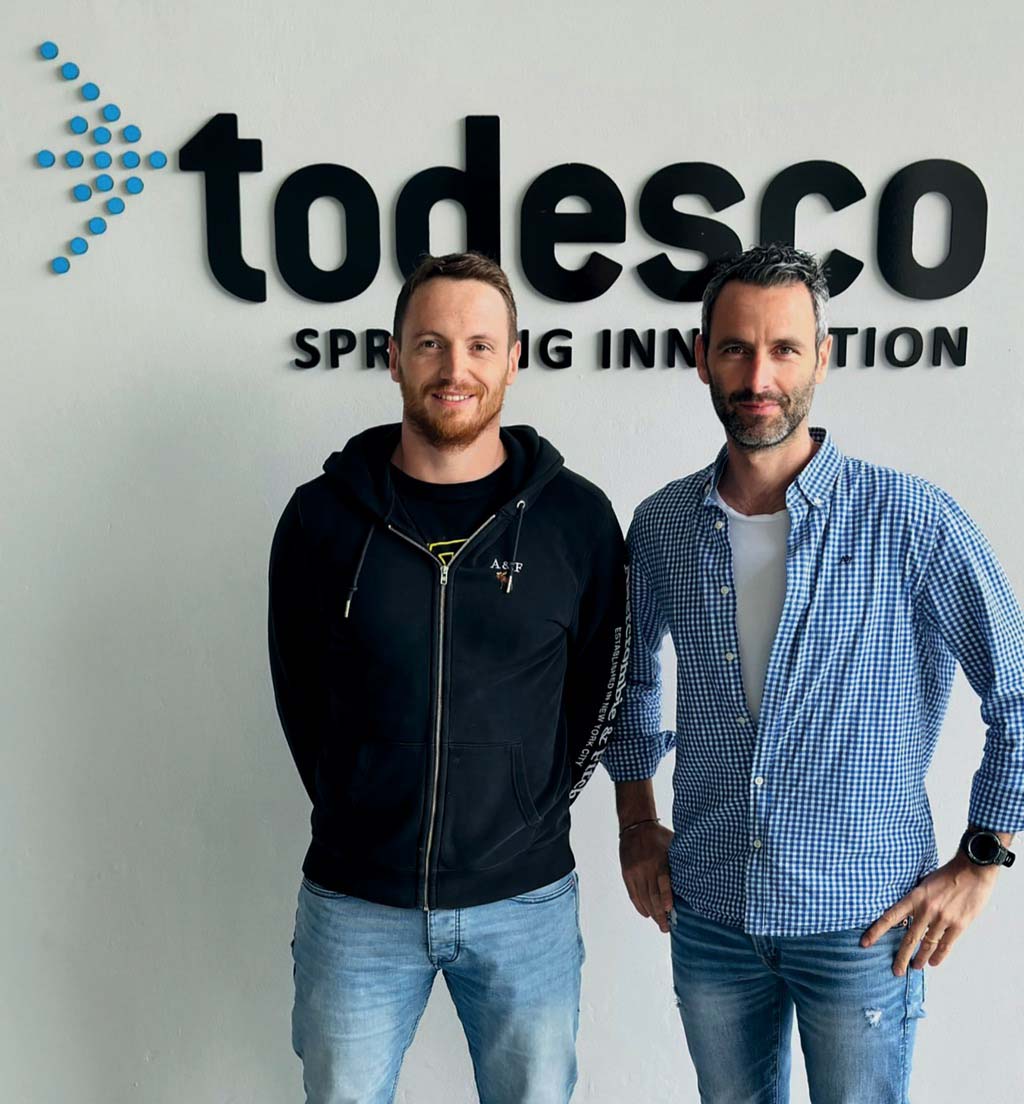
Giorgio e Paolo Todesco
Su quali dinamiche bisognerebbe orientarsi per gli investimenti o forniture all’estero?
“Se una volta si delocalizzava molto la produzione di tecnologia, adesso non è più così conveniente, sia per dinamiche relative ai trasporti, che vedono continue oscillazioni di prezzi, sia per aumentate difficoltà che si potrebbero presentare improvvisamente, come blocchi portuali o difficoltà logistiche. Oltre al rischio sempre costante di sanzioni incrociate tra vari Paesi. Per quanto ci riguarda svilupperemo ulteriormente l’organizzazione produttiva all’estero, in Cina e in Messico, non intese come delocalizzazioni, ma come sedi da cui gestire la produzione locale e le vendite. Sicuramente è finito il tempo in cui, per il basso costo della manodopera, si produceva dall’altra parte parte del mondo per poi rivendere in Italia”.
C’è un obiettivo preciso nell’ambito di questa strategia?
“Soprattutto consolidare la presenza su mercati diversificati. Per quanto ci riguarda lo faremo proprio in Centro America e in Cina, con quest’ultimo che rimane il mercato più interessante al mondo e dove noi siamo riusciti ad assemblare macchine anche durante il periodo del Covid. In questo modo si potranno creare aziende orientali o messicane, di proprietà italiana. La progettazione continuerà ad essere seguita direttamente da qui, nell’ufficio tecnico, sul quale noi da anni stiamo investendo molte risorse sia dal punto di vista economico che come figure professionali”.
Sotto il profilo imprenditoriale quali sono invece le scelte giuste da fare?
“Innanzitutto spingere il più possibile sull’innovazione, sia tecnologica di prodotto che di processo, il discorso ovviamente non riguarda solo il nostro marchio ma tutte le realtà del settore conciario. Allo stato attuale l’attenzione al risparmio del prodotto chimico e alla sostenibilità sono argomenti importanti, non dimenticando però che quello che sbilancia tantissimo nel computo finale è collegato al risparmio del tempo, per un macchinario il costo orario si calcola in migliaia di euro. Alla fine macchine senza un controllo di processo serio, hanno un costo così elevato che non si riesce più a creare redditività”.
Che soluzioni proponete al cliente?
“Lo poniamo di fronte ai numeri reali, analizzando nello specifico quanto costa la produzione per ogni lotto rifinito, quanto ha impattato globalmente e su quanto si può risparmiare con soluzioni avanzate con un vantaggio evidente per quanto riguarda la produttività. Ne è un esempio Speedster 2.0, un macchinario che è in grado di simulare le nostre linee di spruzzatura, con una precisione assoluta, consentendo di testare i risultati del processo di verniciatura su campioni o piccole produzioni senza impegnare la linea principale generando dei fermi produttivi. Speedster 2.0 è una macchina di nuova concezione, frutto di anni di esperienza e presenza continua dei nostri tecnici nei reparti di rifinizione delle pelli, che nasce dalla sintesi di lunghe ed approfondite analisi delle prestazioni produttive delle linee di rifinizione a spruzzo e delle criticità che giornalmente si presentano in tali reparti”.
Quali sono le criticità principali legate ai tempi?
“L’insieme delle attività necessarie per verificare e convalidare la colorimetria e altre caratteristiche estetiche come per esempio l’opacità della pelle: a valle del processo di verniciatura su una linea a spruzzo, richiedono un tempo di esecuzione che mediamente incide per oltre il 30% sull’intera giornata lavorativa. Condizione che si aggrava qualora fosse necessario correggere il colore caricato nelle cabine di spruzzatura, e diventa insostenibile quando non è possibile recuperare e rigenerare il colore non conforme, perdendo così il quantitativo utilizzato per il carico dei circuiti. La tendenza del mercato attuale, che richiede la produzione giornaliera di numerosi articoli anche per metrature esigue, a scapito di lotti mono-prodotto, è un’ulteriore aggravante al miglioramento del processo di lavoro”.
Alla fine come si arriva al controllo totale della macchina?
“Attraverso la produttività delle linee che noi abbiamo individuato con il software denominato Statwatch, sviluppato interamente in azienda, che consente di monitorare in tempo reale le prestazioni produttive dei sistemi di rifinizione Innover e Kingfisher. Si tratta di uno strumento essenziale per ridurre le fasi, controllare in tempi morti nei processi di lavorazione e prevedere preventivamente la manutenzione dei nostri macchinari. I sistemi tradizionali nascono generalmente come applicazioni “parassite” che chiedono l’intervento degli operatori per definire gli stati macchina, come attrezzaggio, produzione e fermo macchina. Spesso tali sistemi di monitoraggio si applicano su macchinari che sono realizzati con componenti fornite da diversi costruttori e per questo non sono governati da una logica e da un linguaggio comune. Non si tratta quindi di una mera analisi dei dati, quanto più di una lettura indiretta di stati di funzionamento”.
Qual è la caratteristica principale del software Statwatch?
“Il fatto che non solo è indipendente dagli operatori, ma fornisce il risultato qualitativo della produzione, individuato nell’OEE (Overall Equipment Effectiveness), e l’impatto ambientale relativo al lotto prodotto nel periodo di riferimento. La dashboard principale rappresenta su scala temporale, generalmente i giorni, il numero di pelli rifinite e il numero di pelli che, senza le inefficienze produttive, sarebbe stato possibile rifinire. Nel contesto dei parametri presi in esame, con il numero realmente realizzato e quello potenziale, oltre alla produzione di pelli, emerge mediamente una reale produttività inferiore al 50%. Oltre a questo, su ogni lotto, stiamo introducendo il rilievo di ogni consumo: prodotto chimico finito sulla pelle, dei litri di acqua impiegati, emissioni in atmosfera, oltre ai costi di energia elettrica e termica. Con questa soluzione il cliente può crearsi una statistica di quelli che sono gli articoli più impattanti dal punto di vista ambientale e soprattutto dal punto di vista produttivo. Tale sistema, in cui risulta strategico ridurre il più possibile i fermi macchina, è molto richiesto soprattutto all’estero, ma anche nei principali distretti italiani della pelle”.
In che modo vengono visualizzate le informazioni sul sistema proposto dalla TODESCO?
“Attraverso i cosiddetti grafici di produzione: i semplici ed intuitivi “grafici a torta” riassumono tutte le fasi operative della linea di rifinizione, all’interno di due stati principali, quello di macchina attrezzata e di macchina non attrezzata. In particolare, quando la macchina è attrezzata, dunque pronta a rifinire, si possono identificare i tempi relativi all’assenza pelli, il tempo perso per eccessivo distanziamento delle pelli nel nastro trasportatore, fino a quello necessario per la spazzolatura e la soffiatura delle pistole. Sono poi riassunte tutte le fasi di attrezzaggio: manutenzione, lavaggio delle pistole, preparazione della macchina per arrivare a rilevare anche l’assenza dell’operatore”.
Dal punto operativo come influisce il software nella gestione del lavoro?
“Statwatch è in grado di interpretare le fasi produttive, e tramite un sofisticato algoritmo, fornire assieme al valore della produzione, espresso in numero pelli ed area totale delle pelli rifinite, il valore della mancata produzione, che scaturisce dalle perdite di tempo che si hanno con macchina attrezzata e pronta a spruzzare. Con la presentazione grafica in un Gantt giornaliero, l’utente può rapidamente verificare quando e dove si sono verificati i fermi produttivi. Attraverso un grafico temporale è inoltre immediato comprendere in quali momenti della giornata si sono presentate le inefficienze produttive. Tutti i dati monitorati sono esportabili con report possono essere ottimizzati per la direzione di produzione o, con maggiori dettagli per l’analista di produzione”.
“l’ufficio tecnico è il cuore dell’azienda” - Giorgio Todesco ricopre il ruolo di Chief Technology Officer: “Qui ogni scelta è condivisa con il team, ogni elemento è spinto a “Think outside the box!”
Oltre che socio assieme al fratello maggiore Paolo, nell’organico dell’azienda di Creazzo, Giorgio Todesco ricopre l’importante ruolo di CTO (Chief Technology Officer) e responsabile dell’ufficio tecnico.
“All’interno della nostra realtà – spiega Giorgio – la condivisione di ogni progetto è corale, tutti sono informati di quanto sta avvenendo e quali sono i progetti in atto. Il fulcro dell’attività è rappresentato dall’ufficio tecnico, dove lavorano 8 specialisti, il cuore aziendale. Il gruppo è composto da 2 ingegneri, oltre a disegnatori, progettisti, programmatori e addetti ai software, ed è qui che si svolge la fase principale di ricerca & sviluppo; a questo ufficio viene destinata la gran parte degli investimenti: a livello di risorse abbiamo deciso di sbilanciare tutto in ricerca e ingegneria, oltre che in tecnici e professionisti specializzati. In archivio abbiamo un autentico “tesoro” composto da circa 20 mila disegni meccanici esclusivi, con tutti i singoli componenti elaborati e progettati da noi. Tanto per dare un’idea di quelli che sono i numeri, a livello di multipli arriviamo ad avere 180-200 mila componenti in un ogni macchinario prodotto dalla Todesco. Strategico è anche il nostro laboratorio interno che garantisce un appoggio per i clienti per testare i nostri macchinari e i loro pellami, oltre che per fare ricerca e puntare sempre a nuovi obiettivi”.
Perché la scelta di disporre di uno staff così compatto?
“Si tratta di una strategia imprenditoriale ben ponderata, portata avanti con successo negli ultimi 15 anni. Il tessuto industriale vicentino, anche nel capoluogo e nel suo hinterland, vanta un’alta industrializzazione, con realtà leader nella meccanica di precisione, elettrotecnica e metalmeccanica, in grado di garantire un elevato know-how e un’attenta gestione dei costi. Pezzi e componenti vengono realizzati da queste aziende terze, scelte tra le eccellenze, in un territorio limitato, un raggio di poche decine di chilometri all’interno della provincia. La scelta di rinunciare alla produzione meccanica interna è avvenuta anche per una questione di spazi che non ci consentirebbero di allestire altri reparti oltre a quelli di cui disponiamo”.
Alla base c’è anche un aspetto economico?
“Indubbiamente sì. Se dovessimo acquistare centri di lavoro per produrre internamente tutte le parti servirebbe un investimento compreso tra i 10 e i 20 milioni di euro, tra l’altro macchine ad elevata obsolescenza. Ma per farlo avremmo la necessità di un organico con 70-100 dipendenti specializzati: assumere specialisti da dedicare alle lavorazioni meccaniche, carpenteria e parti elettriche significherebbe disporre di un’enorme struttura che non ci porterebbe vantaggi. Siamo bravi a progettare, assemblare e installare impianti, e lasciamo fare il resto a chi lo sa fare meglio di noi. Senza dimenticare che, come filosofia imprenditoriale, vogliamo continuare a cambiare, innovare e migliorare. La tecnologia meccanica è in continua evoluzione e in questo modo abbiamo la flessibilità e la possibilità di cambiare i componenti di continuo”.
I vostri sistemi sono apprezzati in quanto sempre innovativi: quanto sono importanti le partnership con le università?
“Molto importanti, in particolare collaboriamo volentieri con quella di Padova. Spesso ci avvaliamo come collaboratori esterni di ricercatori dello stesso ateneo, dove noi ci rechiamo per studiare e sviluppare progetti, ce ne sono tuttora alcuni in atto. Nell’ambito di questa collaborazione seguiamo due spin-off dell’ateneo patavino, nell’ambino della robotica e della fisica, con i quali stiamo sviluppando da una parte alcune macchine e dall’altra l’evoluzione di processi. Capita anche che siano loro a farci visita in azienda, in questo caso si procede solitamente con una simulazione dei programmi nell’ambito di determinate lavorazioni nel nostro laboratorio. Questi tipi di accordi con l’università ci hanno portato ad ottenere finanziamenti e la possibilità di depositare nuovi brevetti: attualmente ne abbiamo 14 attivi, anche internazionali, riguardanti componenti, processi e macchinari. Molto spesso il lavoro di ricerca è lungo, anche nella misura di anni prima di poterli proporre alla nostra clientela, e cerchiamo di essere scrupolosi prima di lanciare un prodotto sul mercato”.
Che regole avete fissato per chi entra in azienda?
“Innanzitutto consideriamo ogni dipendente, nuovo o con noi da tempo, una preziosa risorsa, quindi dobbiamo metterlo nelle condizioni di operare al massimo, anche per il bene del resto del gruppo, visto che tutti devono interagire tra loro. Chi viene destinato all’ufficio tecnico, tanto per fare un esempio concreto, non svolge un’attività sedentaria ma deve saper mettersi in gioco, provando con le sue mani cosa vuol dire montare o avere sbagliato un pezzo. Generalmente chi opera in questo ufficio si sposta spesso in laboratorio, ma viene mandato anche a confrontarsi con i fornitori o fisicamente negli stabilimenti di produzione per accertarsi di persona dei procedimenti in atto: essere aggiornati su macchinari e sistemi di produzione innovativi è fondamentale per una realtà come la nostra che ha come obiettivo quello di alzare l’asticella. Nostro compito è seguire la loro formazione, mantenerli aggiornati con vari corsi tematici e specialistici e farli interagire su diversi tipi di macchinari per non essere focalizzati nel vedere le stesse cose”.
Nel concetto di un team molto coeso, in che modo favorite lo scambio di informazioni?
“Con incontri mirati, praticamente quotidiani ma talvolta anche più volte al giorno, in cui parlare di argomenti vari o situazioni particolari venutesi a creare all’improvviso. Tutto ciò avviene coinvolgendo i vari reparti, ad esempio è importante anche il parere e l’esperienza dei ragazzi che procedono con l’assemblaggio, che ci possono dare indicazioni importanti su problematiche da risolvere assieme ma anche per lanciare nuove idee che poi decidiamo di sperimentare. Tutti i dipendenti coinvolti all’interno dell’azienda partecipano attivamente a queste riunioni, a turno sono mandati ad eseguire sopralluoghi. Ogni elemento del gruppo e spinto a “Think outside the box!” pensare fuori dagli schemi e esprimere liberamente le proprie opinioni e soluzioni. In azienda ovviamente ci sono delle gerarchie e una distribuzione dei compiti: io sono il responsabile tecnico, poi ci sono i responsabili di produzione, del service, dell’organizzazione dei lavori, quindi le varie mansioni e ruoli che interagiscono più spesso con la proprietà”.
Perché è così strategico l’ufficio tecnico?
“Qui parte l’idea e viene sviluppato il progetto, poi seguono l’ingegnerizzazione, lo sviluppo del prodotto, la creazione e il test dei modelli, tutte fasi al termine delle quali avanziamo la richiesta all’esterno dei pezzi. Quando questi ultimi rientrano in sede procediamo con il controllo di qualità, l’assemblaggio e il montaggio, il collaudo e la spedizione, che prevede la consegna chiavi in mano e la consulenza post-vendita. All’interno del nostro ufficio tecnico ci sono due rami. Il primo segue la ricerca, quindi tutto ciò che riguarda lo sviluppo di nuove soluzioni. Il secondo segue invece il cliente e comprende il processo di gestione delle commesse che porta a definire ogni componente, perfettamente schedato ed inserito nel flusso di lavoro gestito via software. Grazie a questa minuziosa preparazione i nostri impianti sono in grado di entrare in produzione dopo poche ore dall’installazione”.
A livello di progettazione come operate?
“Seguendo le richieste del cliente, a seconda delle necessità del nostro settore abbozziamo miglioramenti o nuovi sviluppi che possono portare ad un aumento della qualità del prodotto, a una riduzione di manutenzioni o ad una serie di cambi di processi. In genere le difficoltà dei clienti sono abbastanza comuni, noi le analizziamo e andiamo a implementare i prodotti: i macchinari vengono sempre personalizzati a livello di dimensioni in base alla lavorazione e tipologia della pelle che viene fatta”.
Come procedete per l’installazione degli impianti?
“Ogni macchina viene pensata, disegnata, costruita, montata e collaudata qui da noi, dandoci la sicurezza di ridurre quanto più possibile problematiche in conceria. L’equipaggiamento più complicato è la parte che riguarda le pistole, l’elettronica e l’elettromeccanica, che viene assemblato, collaudato e calibrato con grande cura. Una volta montata nello stabilimento, il cliente è in grado di iniziare a produrre a pieno regime sin dalla prima ora.”.
In azienda come siete organizzati a livello informatico?
“Ogni commessa, che rappresenti un lavoro da fare per un cliente o che sia un ordine di produzione interno, è gestita in maniera informatica dall’inizio alla fine, viene generata una distinta dall’ufficio tecnico, quindi in qualche modo esiste un “progetto che comanda”, che viene implementato attraverso un software di gestione – PLM (acronimo di Product Lifecycle Management, ndr.) – che si interfaccia con il sistema gestionale in modo che siano sempre controllati tutti i dati principali, tra cui il flusso del materiale, lo stato e i costi delle commesse, così come i prelievi. Lo stesso sistema è collegato con il magazzino automatico, quindi a loro volta i prelievi e la preparazione dei componenti sono sempre controllati dal sistema software. Di ogni macchinario sappiamo esattamente, in che modo è stato montato, quando ciò è avvenuto e il nome dell’operatore che è intervenuto. Il mondo conciario è in rapida evoluzione e disporre di un sistema avanzato è fondamentale avendo macchinari importanti installati in tutto il mondo. Ancora adesso ci arrivano richieste per vari componenti, installati da nostro padre negli Anni Ottanta, alle quali riusciamo spesso a trovare una soluzione per non “lasciare a piedi” l’imprenditore o il tecnico che si è rivolto a noi”.
"La storia" - una grande avventura iniziata negli Anni Settanta
“Ci abbiamo pensato, abbiamo progettato, abbiamo provato, abbiamo rifatto tutto da capo. E lo facciamo da due generazioni”. Con queste belle e costruttive parole, riportate nel sito web della TODESCO, può essere ripercorsa la storia aziendale e familiare della società con sede a Creazzo (Vicenza), fondata nel 1971 con il marchio GT Todesco Snc, da Giampietro Todesco, specializzatasi inizialmente nella produzione di apparecchiature con tecnologia ad ultrasuoni per il controllo della spruzzatura sulla pelle.
L’avvio dell’attività attuale, che vede anche la realizzazione di linee complete di verniciatura a spruzzo, in cui attualmente è una delle leader a livello italiano e internazionale, risale in realtà al 1976, anno in cui è iniziata la vera e propria attività industriale in un garage di casa. Da allora si è registrato un crescendo, sia dal punto di vista delle innovazioni tecnologiche, della nascita di nuovi prodotti e della presenza anche nel mercato estero. Fondamentale in tal senso la crescita negli Anni Ottanta, caratterizzata dalla nascita di Microp (oltre 1000 modelli venduti), il primo economizzatore con microprocessore a bordo, dalla crescita nel settore navale, con la consegna di sistemi a spruzzo per il colosso Fincantieri e dell’innovativo “Jetto”, il primo controllore per spruzzatura elettrostatica. Altrettanto significativo lo sviluppo avvenuto nel decennio successivo: al 1990 risale la realizzazione della prima pistola a spruzzo a bassa pressione, modello GTV1, nel 1997 la nascita dell’economizzatore multifunzione “Cometa”, mentre nel 1998 hanno subito riscontrato grande successo le linee complete ad alto risparmio energetico. Sotto il profilo tecnologico decisivi sono stati gli Anni Duemila, con importanti novità subito ben recepite dal mercato nell’ambito delle innovazioni: dal lancio di HV-01 e HV-02, la seconda e terza generazione di pistole a bassa pressione, fino ai moderni sistemi di cambio colore rapido. Fondamentale nello sviluppo della TODESCO è stato il secondo decennio del nuovo secolo, caratterizzato dall’ingresso in azienda della seconda generazione familiare, con Giampietro affiancato dai due figli, Paolo, ora 42enne e Giorgio, 33 anni, poi diventati soci unici. I due fratelli hanno intrapreso entrambi studi specifici prima di entrare nell’organico aziendale: il primo si è laureato in ingegneria elettronica all’università di Padova mentre il più giovane ha conseguito la laurea in ingegneria meccatronica all’ateneo distaccato di Vicenza. Il rilancio definitivo del marchio Todesco risale al 2015, anni in cui è stata proposta sul mercato la linea Innover, primo sistema in assoluto con 24 pistole di spruzzatura e che ancora oggi rappresenta uno dei top della gamma. La linea Innover ha accompagnato altre soluzioni mai impiegate nel settore, in particolare il modello di pistola super HVLP, HV-03 e l’economizzatore Vision con scansione della pelle senza barra di lettura. Il 2020 è stato l’anno di presentazione della macchina per il controllo del colore “Speedster”. Un ulteriore, fondamentale e decisivo passo in avanti, si è registrato nell’attuale decennio, dove l’azienda veneta ha affiancato alla propria presenza alle fiere internazionali del settore, lo sviluppo di nuovi macchinari: Microp Next (ultima generazione di economizzatori che funzionano con un semplice PLC industriale), Speedster 2.0, il sistema a secco per il lavaggio fili in linea RLS-22 e le nuove linee Kingfisher. Per il 2023 si attendono importanti sviluppi nel secondo semestre, in linea con la tradizione di oltre mezzo secolo che continuerà a regalare innovazioni tecnologiche e nuovo proposte non solo per il settore conciario.
GRUPPO VECCHIA TOSCANA-TODESCO, RITROVARSI 40 ANNI DOPO
L’azienda di Fucecchio (Firenze) ha acquistato da pochi mesi una linea completa di spruzzatura Kingfisher prodotta dall’industria vicentina, subito entrata in funzione con ottimi risultati. Un rapporto di fiducia iniziato nel secolo scorso

Paolo Todesco e Francesco Testai, figlio di Valerio, attuale Ceo di Gruppo Vecchia Toscana
Una partnership industriale iniziata a fine Anni Settanta a cui si accomuna un rapporto quasi familiare. E’ un legame che persiste da oltre 40 anni, quello che riguarda il Gruppo conciario Vecchia Toscana Spa di Fucecchio (Firenze) e la Todesco di Creazzo (Vicenza), tornato alla ribalta nei primi mesi 2023 con l’acquisto da parte dell’azienda toscana di una linea completa di spruzzatura, modello Kingfisher, completamente equipaggiata con tecnologia proprietaria Todesco, in particolare con pistole volumetriche HV-02 e l’economizzatore Microp Next, che fa parte del top di gamma dell’industria veneta e ora in funzione nell’area produttiva.
“Tutto iniziò nell’estate del 1977 – il racconto di Valerio Testai, attuale Ceo di Gruppo Vecchia Toscana, a quel tempo studente e non ancora inserito nell’organico aziendale – quando Giampietro Todesco, fondatore dell’omonima azienda, venne nel nostro stabilimento per proporre delle misuratrici elettroniche che mio padre acquistò, dopo aver verificato la qualità. A quel tempo la Todesco (al tempo GT) era nata da poco e muoveva i primi passi nel garage di casa: come loro anche noi, oltre 20 anni prima, avevamo scommesso tutto nell’avvio di un’attività imprenditoriale, partendo praticamente dal nulla, dopo aver acquisito esperienza come dipendenti e operai. In realtà il ricordo più lucido che risale al rapporto con la Todesco è quando il nostro responsabile delle manutenzioni fu mandato a Creazzo per seguire un corso di formazione per poi gestire i nuovi strumenti che avevamo acquistato. Durante l’estate, con le scuole chiuse, ero presente tutto il giorno in conceria e mio padre, che aveva fondato la società nel 1957, all’inizio del boom economico, mi mandava spesso al seguito di queste trasferte, perché era un modo per imparare il mestiere e conoscere nuove realtà. Io, che in quel periodo ero poco più che un ragazzo, andai ad imparare come utilizzare le macchine appena acquistate: ho un piacevole e nitido ricordo di quella esperienza”.
“Il nuovo approccio è avvenuto a distanza di quasi mezzo secolo – conferma il signor Valerio – dopo essere venuti a conoscenza che loro avevano prodotto delle pistole di spruzzatura, dotate di una tecnologia molto evoluta e sofisticata. Così, a metà dello scorso autunno, siamo stati in visita nella sede di Creazzo, dove ci siamo trovati di fronte ad una realtà ben diversa dal garage dove tutto cominciò, caratterizzata dalla continua ricerca di innovazione, quale identità mantenuta dalle nuove generazioni della famiglia Todesco, un vero e proprio laboratorio con tante novità. In particolare ci ha colpito il modello Kingfisher, che è poi quello che abbiamo acquistato per il nostro stabilimento produttivo. Il tessuto economico italiano, soprattutto per quanto avvenuto nel secolo scorso, è rappresentato soprattutto dalle famiglie, anche se non sempre si consolida il cambio generazionale: in realtà in questo caso posso dire che la continuità è stata garantita e sono stati fatti ulteriori passi in avanti”.
“Pur ammettendo di essere di vecchio stampo – continua il Ceo della conceria fiorentina – io prediligo lavorare con le aziende dove alla base ci sono le famiglie, sono loro ad aver contribuito a sviluppare l’Italia e a farla diventare tra le potenze mondiali industriali. Oggi l’economia moderna sta mutando rapidamente, tanti imprenditori italiani non hanno il coraggio di passare l’azienda e talvolta preferiscono cederla ai fondi internazionali in cambio di soldi, ma a mio parere talvolta questo può rappresentare un errore. Rimango un difensore della famiglia in tutti i sensi, la nostra vive l’azienda in maniera profonda, per noi rappresenta una seconda casa”.
Ma perché la scelta di Gruppo Vecchia Toscana di investire nelle tecnologie evolute e sofisticate della Todesco? A rispondere è il figlio Francesco, classe 1989, in azienda dal 2015, dopo aver conseguito la laurea in ingegneria gestionale. “Per una serie di motivi – precisa – innanzitutto la volontà di migliorare la qualità del nostro prodotto, destinato ad un’altissima gamma del mercato, visto che operiamo nella moda e nel lusso, per i settori calzature e pelletteria. Un’altra nostra esigenza, subito riscontrata nella gamma Todesco, era ridurre i consumi energetici, di prodotto chimico e ridurre le emissioni in atmosfera. Con la nuova macchina in linea, peraltro bella ed elegante anche dal punto di vista stilistico, abbiamo iniziato la produzione da inizio aprile, riscontrando sin da subito un risparmio di energia elettrica ma soprattutto di prodotto, rispetto ad una macchina di spruzzatura più datata. Anche a detta dei nostri tecnici il miglioramento è stato immediato a livello di qualità, senza dimenticare che un minor numero di passaggi nella fase di rifinizione, ha comportato una maggiore produttività e un minor spreco di prodotto chimico”.
Una volta entrato in funzione il macchinario nello stabilimento di Fucecchio, tra i vertici delle due aziende è iniziato uno scambio di informazioni riguardanti l’attività produttiva giornaliera e tutti gli altri dati riscontrabili.
“Una collaborazione in questo senso è fondamentale – aggiunge Francesco Testai – in qualche modo rappresenta l’abc del nostro lavoro: il risultato per ottenere un prodotto ottimale è rappresentato da un connubio di tanti fattori, tra cui la macchina, la pelle, il tecnico, il chimico, l’ambiente, quindi è sempre necessario un confronto quasi quotidiano. Dobbiamo aggiungere che siamo stati molto soddisfatti della fase di installazione e messa a punto della macchina, in questa fase siamo stati seguiti molto bene, così pure durante i primi giorni nei quali i nostri tecnici hanno iniziato a produrre le pelli. Nel passaggio tra il vecchio e il nuovo macchinario avevamo preventivato un periodo, tra collaudo, prove e messa a punto, di 3-4 settimane, in realtà grazie all’assistenza, alle istruzioni e al confronto tra i tecnici delle due aziende, la produzione è iniziata nel giro di pochi giorni e non ci sono stati inconvenienti. Con le tempistiche del settore moda, dove tutto è rapido e compresso, questo ha rappresentato un valore aggiunto importante anche in termini economici”.
Tra le due aziende sono ipotizzabili altre possibili accordi in futuro. “Riteniamo che la collaborazione possa continuare – concludono Valerio e Francesco Testai – in quanto siamo convinti che la Todesco continuerà ad essere un’azienda all’avanguardia nella ricerca e nello sviluppo di nuove tecnologie. Nella nostra attività siamo focalizzati in accordi imprenditoriali con poche aziende, dove è importante il rapporto umano e dove è fondamentale affrontare le problematiche in tempi rapidi, la Todesco è sicuramente una di queste. Terremo in considerazione anche possibili accordi quando eventualmente dovremo aggiornare qualche macchinario”.