Founded more than sixty years ago, the Brevetti CEA group from Vicenza, a world leader in the production of inspection machines for injectable pharmaceutical products, has set itself a new challenge in 2019: the creation of a spin-off that aims to be the analogue of Brevetti CEA, but in the automotive or fashion leather sector.
Since 2019 Corium has had a new goal for CEA Patents. What does it consist of?
“Brevetti Corium is the business division of Brevetti CEA Group, which, thanks to its many years of experience in the world of inspection, has devised the first machine for the automatic inspection of hides managed by artificial intelligence. This innovative solution makes it possible to automate and optimize the leather quality control process, accurately detecting defects and creating a virtual copy of the inspected leather. Corium benefits from the expertise and collaboration of other companies in the group, which operate in different technological fields.”
One of your most popular products is the G52 machine. What are its main features and the advantages it offers?
“The G52 is the first machine in the world developed to meet the need for an automatic solution for the inspection and marking of finished leathers, and represents a major technological innovation in the automation of tanning manufacturing processes. Its main advantage is that it automates the selection of hides – an essential step in guaranteeing product quality – from the beginning of the supply chain to all subsequent production stages. The operation of the G52 is based on artificial intelligence using deep learning and computer vision technology to accurately detect leather defects. The machine inspects the grain and flesh side of the leather using super-performance cameras that capture images at a 40um/pixel resolution, including a patented vacuum system that takes care of the transport of the hides, ensuring a flawless spread in front of the cameras. The system creates a virtual copy of the leather, creating a digital map of all the defects, classified by type and severity, indicating for each defect the exact coordinates, dimensions, and areas of leather involved. The performance of the G52 is remarkable, with an exceptional takt time of 14 seconds per skin, including loading, unloading and real-time data processing. There are machines that use adhesives (rot) applied to the skin as reference points to facilitate geopositioning, orientate the skin and optimise cutting. With the Print&Check module and a VDA verification module that allows the leather to be compared with the reference points and any discrepancies or anomalies to be detected, the G52 does not need any stickers because its system automatically marks the hides. A vision box updates the map of defects, corrects their position and sends the exact data to the cutting machine for nesting and for cutting itself. By transferring the digital image with the defect marks detected on the real leather automatically laid out on the cutting machine, the latter is able to recognize the leather and align it with its virtual copy for optimal cutting. Using macro-defects as markers, the AI is able to establish the geographic location of the leather and ensure its traceability; a value that is currently in high demand in the market for its sustainable application, as it makes it possible to verify the quality and origin of the leather, comply with regulations, reduce waste and increase production efficiency.”
What about the W24?
“The W24 is also an innovative and versatile automatic inspection machine, but works with wet-whites or wet-blues. Compared to the G52 it is equipped with more inspection units. Several groups of cameras and illuminators acquire several images with different angles of light, with the aim of highlighting different and complementary characteristics of the leather. I speak of characteristics and not defects because what constitute defects in finished leathers are not always defects in wet leathers. Using special backlighting and different angles of light, the W24 obtains different and complete images of the leather. It captures the images with high-resolution cameras and combines them into one to create the mapping. All this in 14 seconds, while the skin is moving on the roller at a speed of around 25 meters per minute.”
However, your product range doesn’t stop there.
“No, indeed. As mentioned G52 for finished leather inspection and W24 for wet inspection are our flagship products. We have also developed automatic loading systems for finished leathers. We have two types of multi-stakers, one for finished leathers and one for wet leathers. The first is horizontal and has several bays, it automatically positions and transports the hides according to the result of the G52 machine control. We carefully studied the design to obtain one that would allow the skins to be placed accurately, without producing creases or deformations. The multi-staker for the wetskin, instead, is vertical, with six bays to choose from, and we position it immediately downstream of the W24. We then have the marking system mentioned above, the Print&Check, and a module (which can be stand alone or integrated in the G52) which allows sampling and control of the blowing on the leather, by manipulation, without the need to stop the roller. Finally, we also have two solutions for in-line color control, one of which is already commercially available. It is an eight-channel photometer spectrum that checks for color deviations from a specification provided by the client, a system that finds successful application in both the automotive and fashion worlds. Since the client wants to be sure of absolute color control, being able to do this directly in-line is a great leap forward in quality.”
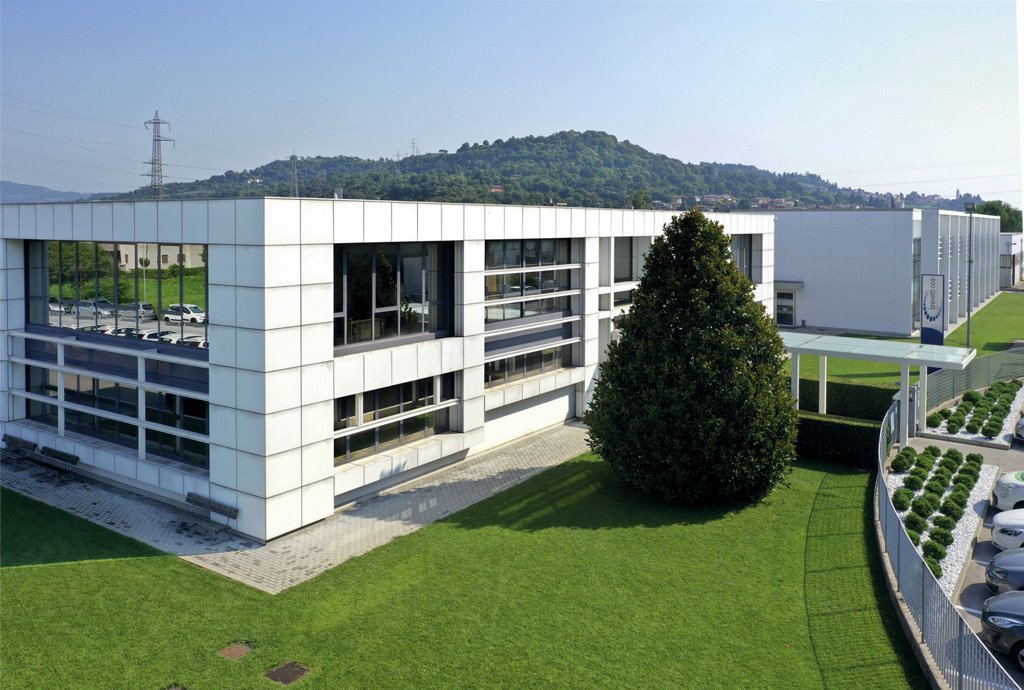
