The Purple system patented by the Creazzo (Vicenza) company and developed together with GSC Group, introduces a new standard in the leather finishing process: it will be featured in Milan at the Tanning Tech 2024 exhibition
The Purple system patented by Todesco of Creazzo (Vicenza) and developed together with GSC Group, another Vicenza company, will be presented at Simac Tanning Tech Pad 18 | Stand G38, scheduled to be held at the Milan Fair from Sept. 17-19, 2024. The Purple system consists of an innovative method of drying and crosslinking fixatives and hybrid topcoats, which also contain a percentage of fixative, in which the temperature of the leather grain does not exceed 35 °C and the catalyzation of the chemical reaction takes place not by thermal effect but by exposure to UV rays. “The advantages introduced by this innovation,” explains Giorgio Todesco, at the head of the family business together with his brother Paolo, “are many, but the main ones are four:
1. cold drying process: the leather remains at a suitable temperature to preserve the natural fibers and this gives a better quality and softness to the finished product; 2. impact on energy consumption on the Carbon Footprint of the leather finishing phase, thanks to the reduction of the process temperature up to 70 °C less;
3. better sustainability thanks to the introduction of chemicals with low environmental impact;
4. reduction of the stickiness of the leather in the end.”
Does UV cross-linking work on non-rigid substrates, though?
“This is a question we are often asked because UV systems are mainly used for wood and metal finishing. The study carried out over the past three years has precisely seen the technical limitations of standard UV compounds being exceeded. By using a UV-reactive fixative, flexural strength requirements are guaranteed, which allows us to say that there is no element of doubt. Among other things, the parameters related to resistance to friction and other more particular ones, such as resistance to alcohol and saline substances, are met. At present, maintaining the standard currently in use in the application of fixatives, in terms of the amount deposited, the tests have all been widely and brilliantly passed.”
An isocyanate-free fixative, right?
“There is one aspect that we did not list above but that is of tremendous importance to us: the system allows the use of UV-responsive cross-linkers, and most importantly, the use of isocyanate is no longer required. As we all know, isocyanate naturally reacts with polyurethanes, in a sense “ glazing.” This chemical reaction, which is so necessary to give the topmost layer of the leather the required physical seals, introduces a no small issue in the handling of machinery. In fact, especially in hot working environments, the chemical compound tends to solidify already inside the pipes and, more particularly, inside the spray guns, the various regulating devices, pumps and in the distribution organs.”
How did you solve the problem?
“Despite the presence of automatic controls for washing all the sensitive parts, it is common that following a temporary production stop, a classic example being a color check, the product contained in the spray booth is no longer usable. Clearly, this is a waste, production inefficiencies and un-budgeted maintenance costs. The use of an isocyanate-free compound completely eliminates the problems listed above, since the chemical reaction, which leads to solidification of the fixative, occurs only if it is subjected to UV radiation.”
What do you expect from this project?
“Definitely a lot. We believe that the Purple system, understood as machinery, chemical and process, can become a new standard, not only in the automotive sector-which is a natural environment for performance coatings-but can also be used for high-end furniture and so also in leather goods and footwear. In fact, the mechanical strength performance we are achieving is such that a minimal amount of product can be deposited on various items, for example on leather used to make bags. This is largely in line with what the market demands: quality and natural grain without, however, sacrificing durability and strength over time.”
Do you have any other news for the market at the fair as Todesco?
“At Simac Tanning Tech we will present the upgrade package of all our existing machinery. In particular, thanks to the new Microp Next machine controller, we are now able to implement total control over the spraying lines, without the operators defining the machine states. Thanks to Statwatch, our Scada software, we are able to provide the client with parameters related to productivity, on the period and on the individual batch, as well as an endless series of other data, which the client can conveniently customize to his needs. In fact, Microp Next provides the ability to connect, to an unlimited extent, any type of sensor that is required: from chemical consumption analysis, to real-time viscosity, rather than air, water, energy consumption. These are key aspects, especially in anticipation of the 5.0 transition.”
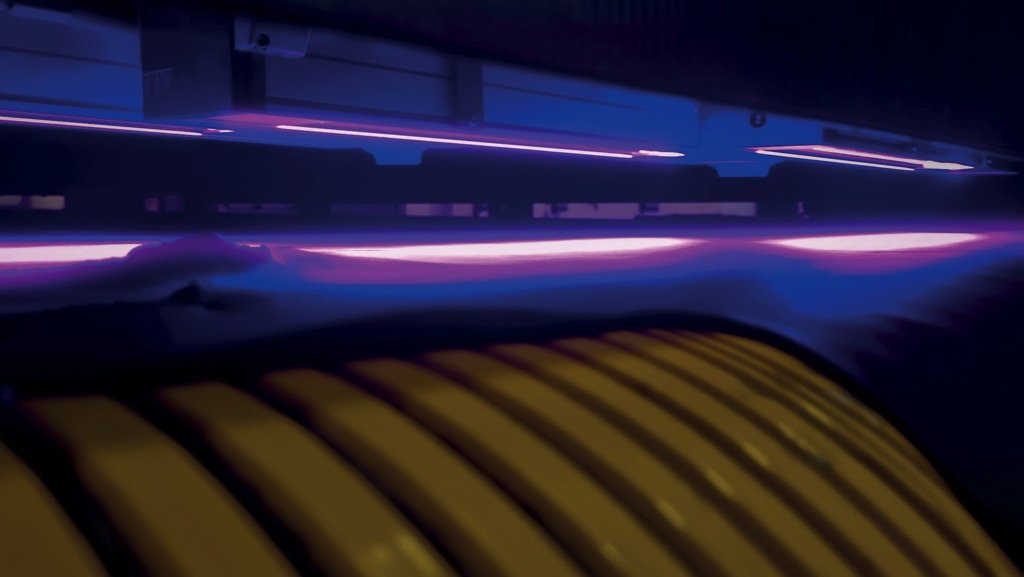
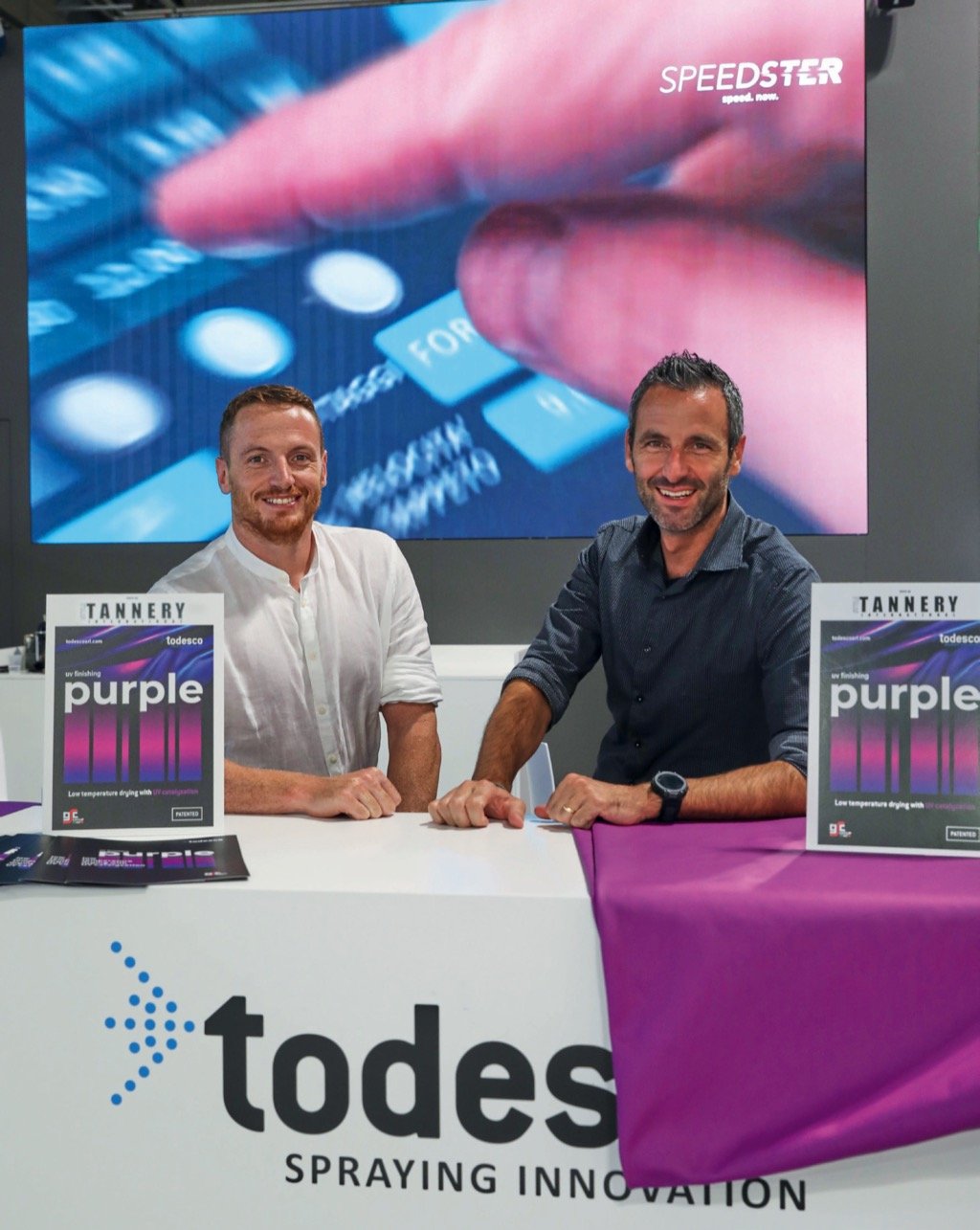
Giorgio and Paolo Todesco at the latest edition of Simac Tanning Tech

Paolo Todesco and Adriano Serafini, CEO of GSC Group
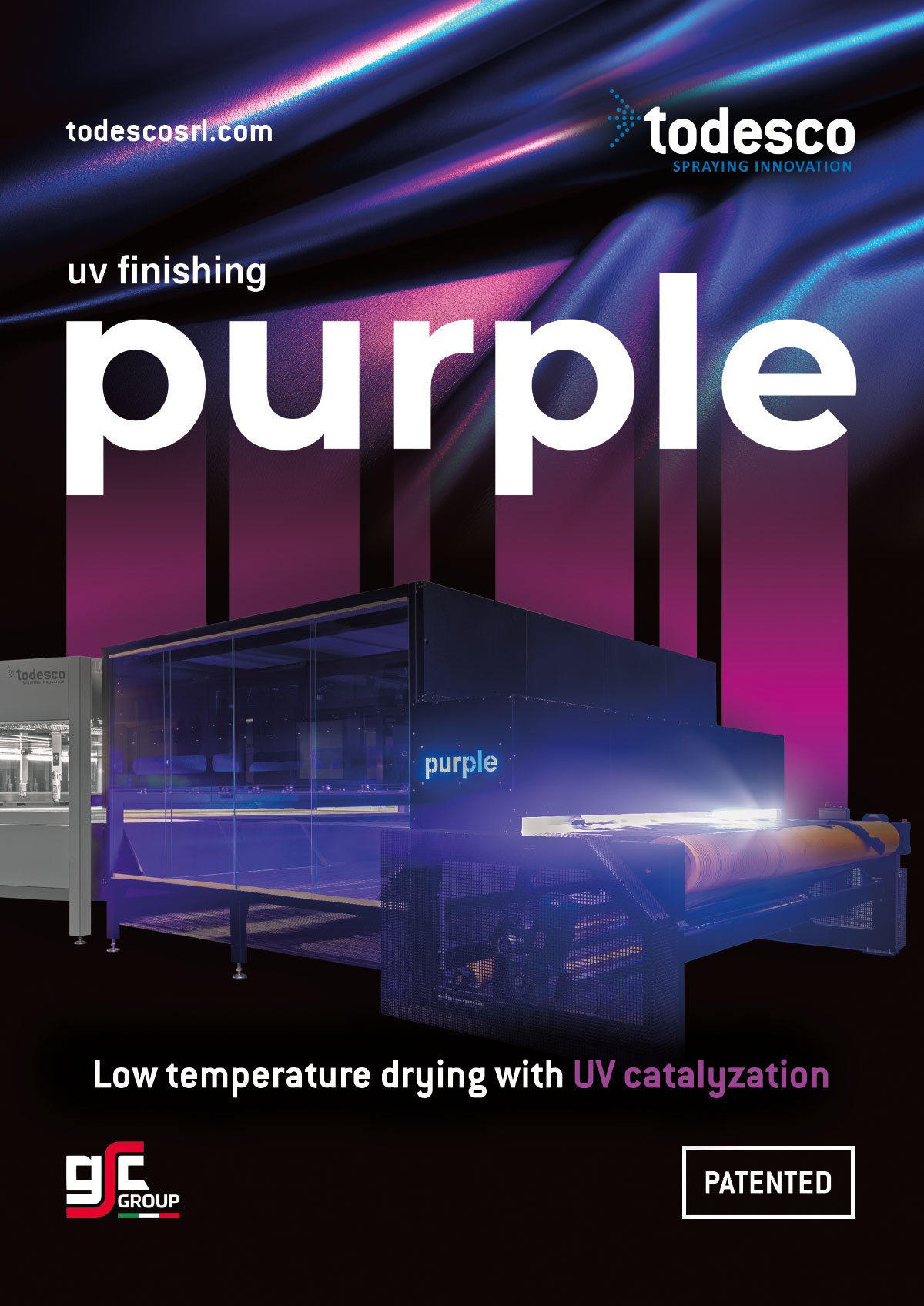