Headquartered in Montorso Vicentino, a town in the Arzignano tanning district, NEXUS showcased at the Tanning Tech exhibition a world-class prototype: it’s a manipulator
The long-awaited moment has finally come for NEXUS. Maybe the most important for the firm headquartered in Montorso Vicentino, a town located in the Arzignano tanning district, and established in 1998, featuring a staff of technicians with a long-standing experience in the industrial automation sector: as a matter of fact, at the latest Tanning Tech edition, it put on display a ground-breaking machine, very similar to a manipulator, set to turn around the tanning industry, thanks to a cutting-edge project technology-wise, boasting level-class innovations. For years, the Veneto-based company led by Mirco Roncolato and Luca Fracasso, co-owners and partners, has been dealing with the design and manufacturing of electrical and electronic equipment for the automation of plants and machinery, devised mainly for the tanning field, but also for other business sectors. In full compliance with the Industry 4.0 standards.
Due to space-related reasons, the prototype was not showcased during the fair, but it remained at the corporate headquarters. Here the owners arranged a series of visits, after the trade show, with groups made up of either a single person or a small number of people, strictly by appointment and by invitation only: in this way, the visitors had the chance to see with their own eyes the machine and to test it, gathering the required pieces of information concerning any detail. We collected some data during the exhibition, given that the owners set up the stand with some screens showing two videos about the functioning machine: the first was devised to arouse curiosity and interest, while the second was more technical and it put in the limelight the prototype’s key characteristics.
“This machine,” explained Mirco Roncolato at the Tanning Tech exhibition, “was tested for a month in one of the most prominent, historic tanneries in Arzignano, then taken back to Nexus to put it on display for the interested customers. The prototype will remain at NEXUS for at least three years, so as to comply with the international R&D rules and to try out the constant upgrades implemented. We have already received some orders from the leading local enterprises, that will be handled in the early months of 2022. Nevertheless, the situation is steadily evolving, given that, thanks to this cutting-edge concept, a new, interesting “scenario” has taken shape.”
How can we define this new manipulator?
“It is a more advanced stacker, approximately three meters long, completely different from the current trends, because it develops height-wise. The highly innovative system allows to take leather “upstream” from a machine, either a staking machine or a press, and in this way, it can be placed in the gantry. However, the complete project also entails the chance of setting down the material on the loading bed or on multiple gantries (up to three). The gantry option, with different sizes according to one’s requirements, is suitable for large-sized hides, up to the three and a half meters, used mainly in the furnishing and automotive sectors. At the moment, the best performances regard larger leathers, while, for smaller ones, the design phase is currently underway. Besides boasting an eye-catching appearance, the machine features a top-notch leather laying quality.”
What are its distinctive technical features?
“The machine is lightweight and lean, made with fine, sophisticated materials such as carbon fibre. Special attention has been paid to mechanical design, down to the smallest detail, thanks to the use of cutting-edge CAD 3D software, inspired by aircraft-naval mechanics. Another interesting characteristic lies in the machine’s rapid “pliability”, thus resulting in a higher exportability. Its weight is low, less than 18 quintals; therefore, it does not require the employment of cumbersome, expensive cranes, given that it can be moved with a simple forklift truck. As for its export, a smaller case is enough, ensuring a marked decrease in shipping costs. Currently, on the market, a machine with the same performances ranges from 6 to 9 meters length-wise and a width amounting to three and a half meters.”
Can you tell us something about its functioning?
“Clearly I can’t reveal some design secrets. I can only say that the machine functions automatically, it figures out the shape of leather, the structure and placement of the gantry. There is the opportunity of an automatic synchronism with the speed of the machine upstream. The new functional concept has led to the elimination of the leather “dragging” principle: even if the type of leather varies, smooth or wrinkled, stiff or soft, its placement does not change. That’s why, this technology manages to effectively lay down hides that can be difficult to manage such as the highly polished ones for the automotive sector. Therefore, the machine succeeds in assessing the shape of leather (front, back end), thus guaranteeing top-notch performances and results.”
Can you reveal us some secrets?
“Let’s just say that several secrets are hidden inside a column: however, we can neither reveal them, nor put them on display during “live” visits. For this project, entirely patented, we have invested substantial resources and many months of study and work, both for the whole machine and for the singular components. And yet, we believe that the prototype can be further improved over time. One of our strategies will revolve around the selection of partners to keep working together, also out of respect for those that have been cooperating with us so far. A significant collaboration will be established with the most prominent tanneries, the latter acting as a source of suggestions for the upgrade of the machine.”
Is there a detail you have paid closer attention to?
“To safety, in full agreement with the tanning entrepreneurs we have cooperating with. The machine stands on its own, but it is fastened to the floor to guarantee higher safety standards: the protruding part, that is, the arm, weighs just five and a half kilos, and, if we consider, for instance, five kilos of leather, we have a difference of approximately 10 kilos, wholly supported by the base. Furthermore, the braking system differs from the handling one design-wise. We have also provided implemented a technology that, in case of emergency, moves the machine’s mobile arm away from the dangerous spot. All the safety devices are fully compliant with the current regulations.”
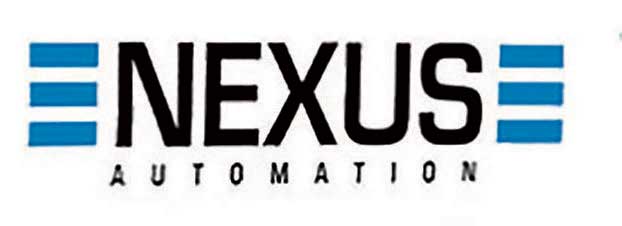
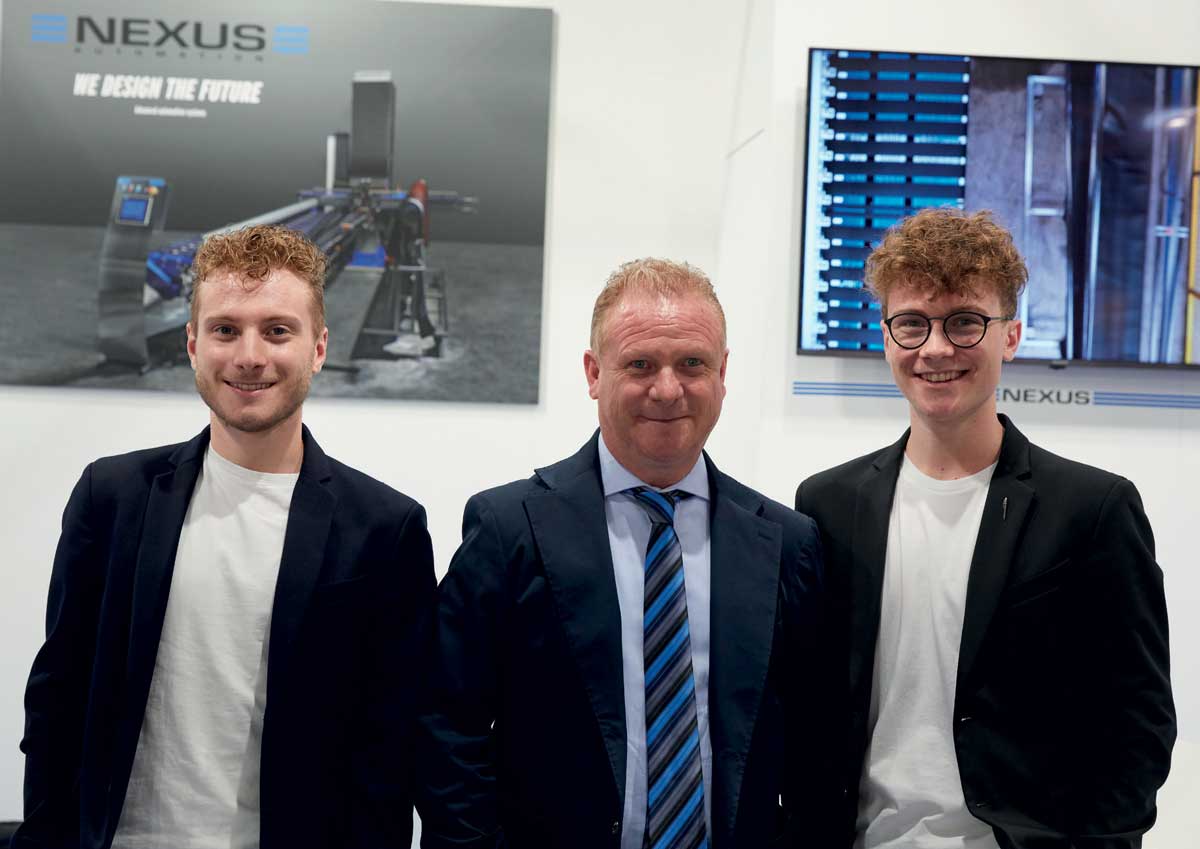
Mirco Roncolato con i figli