Excessive shoe consumption generates billions of wastes but the new frontier of sustainability has been reached thanks to the visionary partnership between Gruppo Lonati, Decathlon and HP.
Lonati Group, HP and Decathlon have joined forces to present an innovative footwear production concept at the latest ITMA in Milan. Exploiting the Muti Jet Fusion from HP and knitting machines from Santoni-Lonati, the aim is to revolutionise the footwear production process by creating sustainable, lightweight and durable shoes. Shoe production is a sector that places a heavy burden on the environment and our health, in fact, according to World Trade Organisation (WTO) estimates, around 23.2 billion pairs of shoes will be produced worldwide in 2021 alone. The footwear industry must find sustainable solutions to reduce, recover and recycle waste efficiently.
It is necessary to create products in a different way, using digital technologies to define the future of manufacturing. This is precisely the spirit behind the collaboration between the three giants: ‘Together, we have developed an innovative and sustainable approach to footwear production that is destined to reshape the entire industry,’ says Patrick Silva Szatkowski, Head of Marketing, Communications and Business Development at Santoni. ‘Traditionally, footwear production requires numerous parts, adhesive materials and a significant workforce. However, we have revolutionised the process by harnessing our technologies and the power of 3D printing.” Their latest innovation is a sports shoe by Decathlon that embodies the future of global footwear production. This innovative shoe, called Traxium Compressor, combines the sock mechanically machined by the Lonati Group’s machines with an innovative midsole and outsole produced with HP’s advanced 3D printer.
The XT-MACHINE knitting machines from Santoni and Double Cylinder from Lonati make it possible to produce uppers with single or double layer fabric, resulting in an integrated upper that offers unrivalled comfort, lightness, performance and quality. In just five minutes and with no waste threads. The HP Jet Fusion 5200 printer produces both the midsole and sole of the shoe, demonstrating the cutting-edge capabilities of 3D printing technology. To ensure optimal performance, these components are made from BASF Ultrasint TPU01 material, a versatile thermoplastic polyurethane powder known for its exceptional shock absorption and flexibility. By integrating these advanced materials and technologies, the sports footwear industry will be completely renewed, paving the way for innovative designs that offer unparalleled comfort, durability and performance. However, this is not the only message the three companies would like to share.
This partnership also aims to stimulate the use of 3D printing and digital knitting for manufacturing at an industrial level. “This approach offers numerous advantages, including the customisation of footwear according to consumer preferences and needs, the repairability of shoes in the event of damage and the reduction of waste through the use of a single material, TPU (thermoplastic polyurethane). In addition, this production method allows for optimised shelf life and on-demand production, reducing waste. 3D printing also offers the possibility to produce locally, reducing transport emissions and supporting local economies. Their latest creation proves that circular production is possible and that waste can become the raw material of tomorrow. Technology can be a key tool to reduce the impact of industry on health and the environment, and this is an important step towards a more sustainable future.
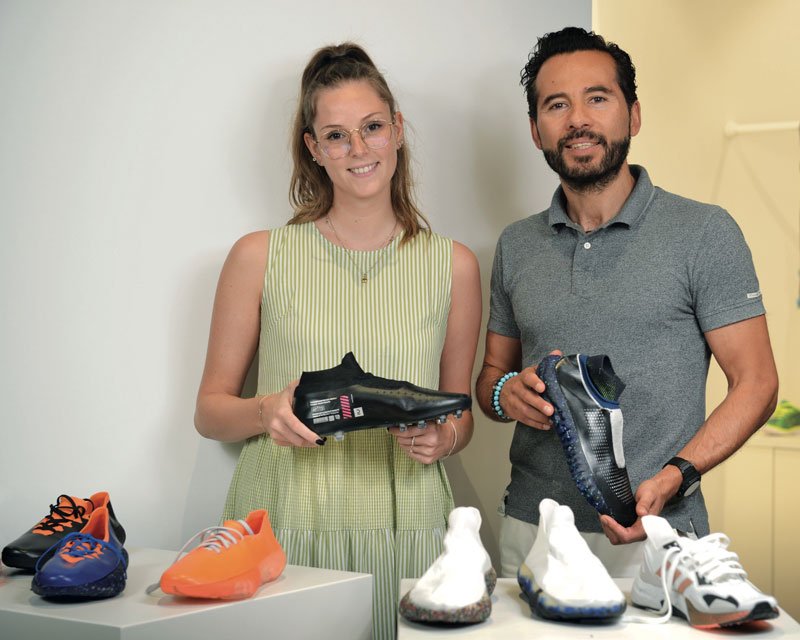
Patrick Silva Szatkowski